Spring 2022 Design Day
Our Spring 2022 Engineering Design Day event will be held on Wednesday, May 4, 2022, from 1:00pm-4:30pm in Montezuma Hall in the Aztec Student Union.
Please view our 2022 Design Day Booklet which provides a picture and description of all projects that will be participating in the 2022 event.
Design Day is the largest College of Engineering event and it showcases the exciting and innovative design projects that our undergraduate Engineering students conceive, design and build during the academic year. Each Senior Design classes in Aerospace Engineering, Civil, Construction & Environmental Engineering, Electrical & Computer Engineering, and Mechanical Engineering will be participating. 73 projects will be showcased at the 2022 Engineering Design Day event. Below are the Mechanical Engineering Senior Design projects that will be showcased at the event (More details of individual projects will be available as the event draws closer).
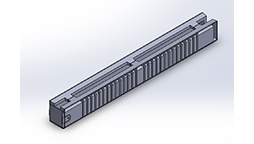
This project, sponsored by Dexcom, has developed a new reusable tray to hold and dispense Instructions For Use (IFUs), an essential component to Dexcom’s Continuous Glucose Monitor packaging, into Dexcom’s automated assembly line. In contrast to the currently used corrugated tray this reusable thermoformed tray will provide an opportunity for future cost savings while offering an environmentally friendly alternative to the current single use tray.
Team members: Diana Arreola, Isabella Enciso, Cameron O'Connell, Brian Peticolas, Amy Turnland
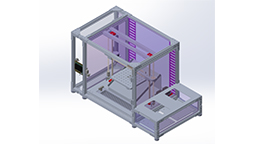
Devices used in a medical setting must have proper labeling on the exterior casing to maintain FDA certification. Team All Suds No Duds worked with sponsor Masimo to create a test device that will be capable of completing up to 100,000 cycles autonomously to test material degradation of devices. This device consists of multiple subsystems for linear motion, drainage, wiping, camera, chemical application, and electrical components.
Team Members: Abdulaziz Alrshaid (ECE), Jason Babayev (ECE), Ahmad Bandar (ECE), Jackson Cruise (ME), Sean Eckstein (ME), Luka Emrashvili (ECE), Lauren Jansen (ME), Jared Meeks (ME), Kamar Mirza Hussein (ECE), Lori Voong (ME)
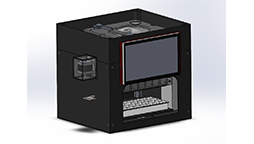
Team Licensed to Pill designed and manufactured an automated pill dispenser to ease the process and reduce the need for fine motor skills for patients and caregivers when dispensing pills into a pill organizer. The pill dispenser is able to distribute a desired amount of pills to their respective days in both weekly and monthly pill organizers, can accommodate a variety of pill shapes and sizes, and has an easy to use, high contrast Graphical User Interface.
Team Members: Courtney Baugh (ME) Julian Ditona (ECE), Kimberly Duron (ECE), Ziyad Elfar (ME), Max Greiner (ME), Isomiddin Kamilov (ECE), Jason Kassissieh (ME), Mark Le (ECE), Ryan Shimizu (ECE), Ethan Tallorin (ME)
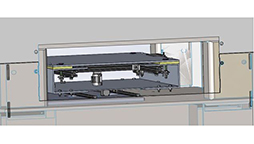
Nordson ASYMTEK dispensing systems provide automation for the semiconductor electronics market where glues and adhesives are applied to electronic assemblies. These can be at the board level, wafer level, or at a package level. This project provides an automated loading, fixturing, heating, and unloading mechanism. The objectives are to (1) provide a fixed "load" and "unload" position(s) to receive a substrate, and (2) provide a fixture to hold and heat the substrate during dispensing.
Team Members: Courtney Baugh (ME), Julian Ditona (ECE), Kimberly Duron (ECE), Ziyad Elfar (ME), Max Greiner (ME) Isomiddin Kamilov (ECE), Jason Kassissieh (ME), Mark Le (ECE) Ryan Shimizu (ECE) Ethan Tallorin (ME)
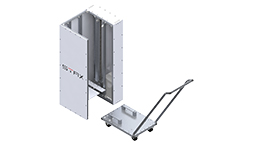
The Stax Engineering team, along with the sponsorship of Masimo, has developed the Automated Tray Tacker & De-stacker with the intent to improve the efficiency of Masimo’s production line. The machine’s design is similar to a 3D printer, where it utilizes rotational motion and converts it into linear motion through the use of a stepper motor, microcontroller, and Lead Screw. As a joint ME/ECE team, we were able to develop an automated mechatronic system that includes sensors, emergency protocols, and a touchscreen.
Team Members: Ali Al-Azmi (ECE), Saud Al-Mutairi (ECE), Faakhir Ali (ME), Ian Estacio (ME), Steven Magayanes (ME), Karim Omara (ECE), Joel Osuna (ME), Alejandro Ortiz (ECE), Chaitanya Patel (ECE), Kevin Uy (ME)
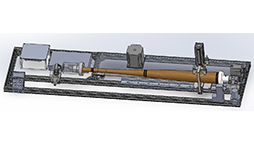
The objective of this project is to design and fabricate a device that increases the hardness and surface finish of a wooden, professional league baseball bat by rubbing along the barrel with a harder material. The design employs a pneumatic cylinder to apply pressure to the bat barrel and two stepper motors to rotate the bat and move the pneumatic cylinder along the bat barrel. This system has been designed to operate at adjustable bat diameters and lengths offered by Vander Pro Sports.
Team Members; Abdulwahab Altawheed (ECE), Vincent Chang (ME), Audrey Paris Chuakay (ECE), Anthony Gugg (ME), Scot Haury (ME), Steven Matti (ECE), Devin Morningstar (ME), Loran Najjar (ECE), Pat Petel (ME), Brandon Pola (ECE)
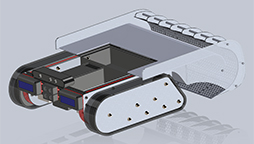
The goal of this project is to design, fabricate, and test a robot that is capable of autonomously traveling across a beach while collecting debris that could be potentially harmful to the environment and surrounding wildlife. The robot is designed to avoid obstacles and return to the home base to safely dispose of the debris that has been found on the beach.
Team Members: Ben Hayenga, Kyrel Polifrone, Matthew Blackmun, Spencer Dickson, Jason Bethmann
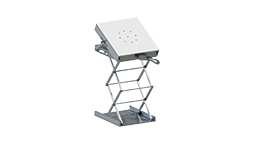
Team MechX was tasked with upgrading the current staging system at the ASML Extreme Ultraviolet research chamber. The actuator introduces additional degrees of freedom adhering to vacuum chamber guidelines. The design consists of simple machines to help position a breadboard used to hold testing materials. This improves the cycle times of testing periods and increases the accuracy of test results. Additionally, positioning the actuator can be completed with a motor-operated wirelessly from a phone app.
Team Members: Andy Huynh, Xikai Xie, Matthew Dacayo, Sidney Palomino
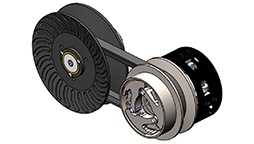
Aztec Baja’s SAE vehicle competes each year in the SAE Baja collegiate series, where various aspects of the vehicle are tested. The Aztec vehicle utilizes a continuously variable transmission (CVT), which is prone to belt slippage at low speeds. Team Belted Bandits has designed and engineered a system to decouple the engine shaft from the primary pulley. Consequently, this improves the output power and maintains the previous vehicle’s top speed. Furthermore, the system complies with the 2021-2022 SAE rulebook.
Team Members: Erika Short, Isaac Miller, Jorge Lacbain, Ciara Garrison, Kedar Kale
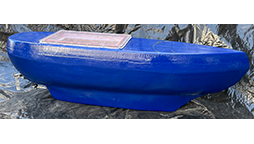
Transnational Criminal Organizations (TCOs) are using autonomous surface vessels to transport contraband undetected across the US-Mexico Maritime Boundary Line. Such vessels are difficult to detect, so they pose a threat to national security. Therefore, the United States Coast Guard requires a fully autonomous vessel under a materials budget of $700 that is similar to previously seized vessels and is as advanced as possible in order to determine the best method to detect them before they reach their destination.
Team Members: Ahren Kimo Aguinaldo (ECE), Frank Aosman (ECE), Abdulaziz Bandar (ECE), Shane Cooke (ME), Jason Lin (ECE), Jorge Martinez (ME), Kyle McCoy (ME), Ivan Orozco (ECE), Andrew Preece (ME), Juan Rojas (ME)
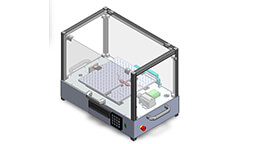
Connector Resistance and Force Tester (C.R.A.F.T.) is an electrically integrated linear mating cycle test system capable of measuring insertion/removal forces and electrical resistance of connectors of various shapes and sizes. This system was designed for Masimo, a medical device company focused mainly on noninvasive patient monitoring, with the purpose of testing their multiple connectors’ lifespan and their mechanical and electrical properties. C.R.A.F.T. is a benchtop sized, fully enclosed system, designed with both mechanical and electrical components. With a user-friendly interface, C.R.A.F.T allows the operator to determine customized parameters for each connector during setup such as cycle speed, travel distance, and connection time.
Team Members: Fahad Alsahli (ECE), Mark Blair (ECE), Jeffrey Calimbahin (ECE), Thomas Floisand (ME), Andrew Jefferson (ECE), Christine Maryfield (ME), Belinda Nguyen (ECE), Jake Prittie (ME), Nereyda Lopez Resendiz (ME), Han Tang (ME)
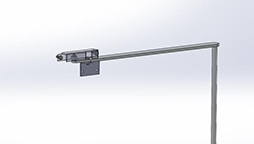
This project involved the design, fabrication and testing of a fully mechanical leverage mechanism that allows field technicians to easily and safely open positively and negatively pressurized doors on Solar Turbines' T130 engine enclosures. With this mechanism, operators can access enclosed machinery without having to shut off the enclosure ventilation system to neutralize the pressure. The mechanism utilizes leverage to create a large push/pull force (depending on the pressure scenario) as a result of a small pull/push force from the operator.
Team Members Nhat Hoang, Abel Napoleon, William Ramirez, Cesar Tellez Ornelas, Le Tung
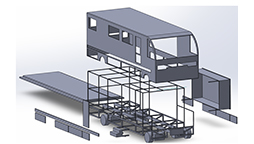
This project involved a system design for a class A, fully electric powered Recreational Vehicle (RV). The team's primary focus was on the powertrain with a secondary focus on structure and exterior. The innovative RV design accommodates 5ft modular structural increments within the vehicle class, and integrates interior customization with slide and lock systems for customer preference. The system includes the integration of cutting edge solar panels for maximum user experience. An exterior wall section providing enhanced thermal and noise insulation over modern examples, as well as 1/12th scale of vehicle design is provided.
Team Members: Philip Alberti, Ramil Gapuz, Justin Legaspi, Rene Navarro, Ryan Sternberg
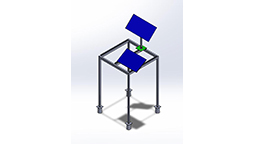
The purpose of the GPS Based Solar is to maximize the efficiency of a solar panel using only GPS coordinates and time. The design solution enables automated panel rotation on two axes so that it maintains a constant orthogonal position to the sun. The power collected from the rotational solar panel will then be compared to the power collected from a stationary solar panel in order to determine the efficiency of the two panels.
Team Members:
Casper Abbasi, Weston Bourgeois, Ava James, Sarah Salgado, Brandon Welsch
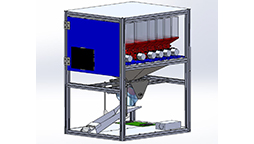
This project involved the design, fabrication and tesing of a consumer, self-serve granola dispensing kiosk. The design solution takes into consideration the customer's ingredient choices as well as the desired serving size. It then uses its control system to maneuver all the mechanical components responsible for measuring, mixing, and dispensing the granola. The secondary goal of this project is to provide a modular design that may be utilized in future kiosks that D&K may be looking to manufacture.
Team Members: Kimo Barrere (ECE), Paris Bee (ME), Adhel AJ Corpuz (ME), Claudia Callejas Dominguez (ECE), Conrado Dela Rosa (ECE), Joe Huang (ECE), Daniel Izarraras (ME), Xavier Lovato (ME), Zayne Mirza (ME), Evaristo Rodriguez (ECE)
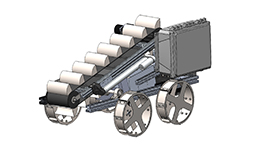
Team HADES is representing San Diego State University at the NASA Robotic Mining Competition (RMC) Lunabotics 2022 by designing, building, and operating a lunar mining robot. The goal of NASA RMC is to find innovative solutions to extract material from beneath the lunar surface using a partially autonomous robot with a dust-free operation/design. The competition is an engineering challenge in which students gain experience with the engineering lifecycle process, from concept development to system closeout.
Team Members: Sterling Belaire (ME), William (Billy) Bilicki (ME), Alyssa Brunen (ME), Andrew Chung (ECE), Linda Clark (ME), Nathan de Chambeau (ME), Josh Dolled (ECE), Jaquelyn Fernandez-Iniguez (ECE), John Paul Edwin Ventura (ECE), Jean Michel Vives (ECE)
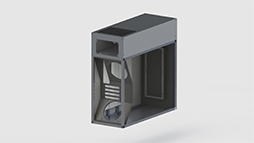
This project is for the development of a personal computer case with improved cooling capability over current market models. Using airflow as the main method of cooling, various fan and component configurations were explored to achieve the current model. With high airflow, dust filtration, and a large component space for customizability, this PC case aims to compete with other models on the current market.
Team Members: Biruck Haleform, Matthew Robert Ilagan, Xavier Leasau, Brett Shultheis, Leonardo Zuniga
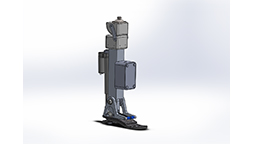
Most current powered prosthetics serve the purpose of assisting the user with their everyday walking. Our team was challenged to design a more advanced prosthetic capable of going on long hiking and hunting expeditions in inclement weather. Our prosthetic uses a linear actuator in series with a spring to provide powered assistance to the user’s gait, making it easier and more comfortable for them to hike and walk on uneven terrain.
Team Members: Nasser Almarshoud (ECE), Susana Arellano (ME), Dina Batros (ECE), Matthew Blake (ME), Zachary Brueggeman (ME), Marc Anthony Do (ME), Garrett Grommes (ME), Justin Killam (ECE), Jarel-John Macanas (ECE), Sony Shosani (ECE)
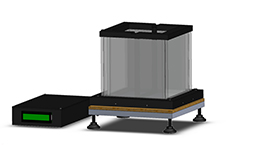
An experimental system was developed to support research by Dr. Amneet Pal Bhalla (SDSU) to develop a numerical model for Selective Laser Sintering (SLS). Starting from a simplistic approach, the phase change interfaces between gaseous, liquid, and solid phases are studied to understand and model how the displacements of such interfaces are influenced by temperature and time. Four experiments are considered.
Team Members: Elias Garcia, Robert Laski, Michael Kassissieh, Jordan Lowe, Daniel Mandujano
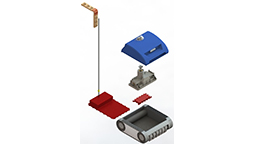
Current robotic pool cleaners exist as either hard-wired to an external power source or battery operated with manual periodic charging, similar to current robotic home vacuums. The project researched inductive charging methods, pool cleaning technologies and various regulatory and practicality concerns. The team designed and fabricated a working prototype of an inductive charging system for Fluidra’s robotic pool cleaner.
Team Members: Abdulmohsen Alabdulkarim (ECE), Aeron Joshua Gonzalves (ECE), Mohammed Mohammed (ECE), Uriel Molano (ECE), Paul Nguyen (ME), Truong Nguyen (ME), Rene Orellana (ECE), Alejandro Ortuno (ME), K'Von Tanner (ME), Shane Wegener (ME)
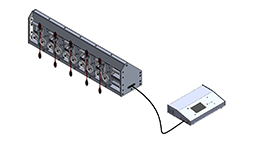
The Electrically Integrated Cable Bend Cycle Test System is designed to test the durability of medical-grade cables manufactured by Masimo. Our device features five independently controlled motorized workstations to carry out flexion stress tests and comes equipped with fully automated testing procedures. Key technologies built into the device include: precision motor control, adjustable workstations coupled with an ergonomic cable mounting system and continuity detection.
Team Members: Abdulwahab Alqurtas (ECE), Kyle Collins (ME), Grace Fraser (ME), Brandon Lipscomb (ME), Joseph Marquez (ECE), Christopher Martin (ME), Jeremy Minimo (ECE), Alfonso Monroy (ECE), Phummin Rotphan (ME), Frank Slewa (ECE)
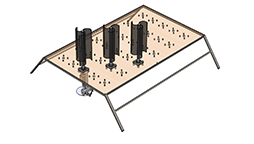
This project supports wind energy research and involves strategically placing multiple vertical axis wind turbines (VAWTs) in a shaded formation to determine ways to improve wind turbine power production efficiency. The project team mapped the boundary layer parameters of the low-speed wind tunnel as a function of the motor speed to determine the optimum placement of the turbine. The project included manufacturing three VAWTs that will be utilized to evaluate the impact of the turbine’s rpm on the downstream behavior of the SDSU Mechanical Engineering Open-Circuit Low-Speed Wind Tunnel.
Team Members: Nicholas Lim, Shaunt Malloian, Jake Marino, Brayan Mota Lopez, Carlos Verdeja
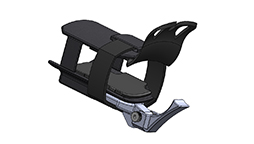
A 36 year-old Army National Guard Combat Engineer was injured in 2004 by a suicide bomb. He sustained multiple injuries including a thumb amputation on his right hand which provides continuous pain and difficulty gripping. He does enjoy mountain bike riding and needs a device to assist with grip, standard riding movements and quick release but does not interfere with use of bike controls or motion in his fingers or palm. With our device, he is able to ride his bike with ease.
Team Members: Caroline Duong, Amber McGrogan, Blake Motley, Tighe Reed, Ethan Short
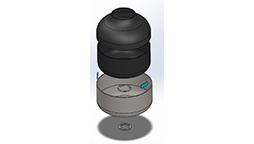
Osseointegration is an operation that provides amputees with an easy attachment point for a prosthetic. Osseointegration patients are left with an open stoma around the abutment, meaning it cannot be exposed to brown water. The objective of this project is to design and manufacture a waterproof cover to be worn during physical activity. The cover shall allow the patient to continue his passion for whitewater rafting and swimming with a prosthetic still attached. Aubrey Benjamin, Kyle Grant, Brody Harris, Nolan McRae, Joshua Norton
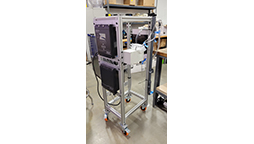
To test the quality of filters, Fluidra performs tests in accordance with the NSF 50 standard for pool equipment. For this, the team was tasked with designing a system capable of measuring the particle size/count in the water at the inlet and outlet of a filter, be able to draw water from two tanks, measure and throttle the flow rate in the system, measure the pressure across a filter, read the temperature of the water, and measure the turbidity (measured in NTUs) at the inlet and outlet of the filter, all in real-time.
Ameer Alhelli (ECE), Ahmad Ali (ECE), Nicholas Davis (ME), Zachary McGraw (ME), Kevin Nguyen (ECE), Laith Noeil (ECE), Christopher Torres (ME), Brian Tran (ME), Kenny Truong (ECE), Jose Maldonado Villarreal (ME)
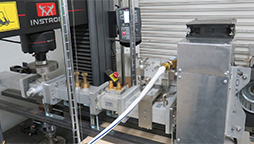
In support of SDSU materials search, team Sintering Engineers have created a sintering chamber that includes a Proportional–Integral–Derivative (PID) controller system for an existing Microwave Press. The PID controller will utilize input data from the materials' increase in temperature and difference in the emitted and reflected power over time, to govern the energy emitted from the magnetron. The intention is to flash sinter a powder based material, under pressure to create more homogeneously transparent material and progress microwave sintering technology.
Team members: Omar Alshatti (ECE), Logan Beltz (ECE), Gabriel Facco Bettinelli (ECE), Dante Gonzalez Corbett (ECE), Aquin Manners (ME), Christopher Sarabia (ME), Eric Segura (ME), Jimmy Tran (ECE)
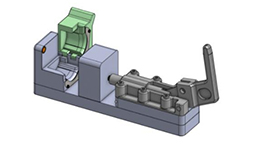
The Dex5 team has designed a fixture that allows production operators to easily conduct a pressure decay test required to confirm production equipment while reducing overall test set up time and steps, and producing a reliable and repeatable result.
Team Members: Gabrielle Ahad, Victoria Carlson, Jonas Marave, Clint Panian, Andrew Silva
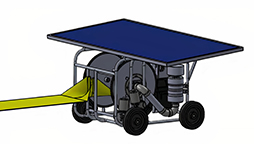
The Rapid Deployment Runway Closure System is an inflatable system developed to quickly deploy and retract to prevent the landing of unauthorized aircraft on remote airstrips by exhibiting the appearance of a barrier. The inflatable is anchored by a ground stake and an off-the-airstrip housing complex containing the blower, power supply, and control system. The system was engineered to be operable by a single person and adhere to airstrip safety protocols.
Team Members:
Sean Connolly (ECE), Alyssa Elkins (ME), Khalid Nunow (ECE), Jomari Paguia (ECE), Marc Tanwangco (ECE), Timothy Turner (ME), Nick Wolford (ME), Bianca Yousif (ECE), Ala Zeidan (ME)
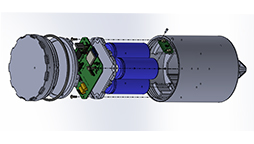
California coastlines have awe inspiring world class beauty, however cliff bluffs with hidden dangers put public safety at risk. Our solution is to deploy a long range underground wireless sensor probe network capable of localized real-time event data processing of: seismic data, tilt changes, temperature and soil conductivity. Our system is both wireless rechargeable, and has redundant wireless data download pathways to maximize operational longevity.
Team Members: Po-Hsien Chen (ME), Eliott Giberson (ME), Nicolas Kano (ME), Kassandra Marquez (ECE), Adrian Melgoza (ME), George Mirza (ME), Tristan Schultz (ECE), Richard Stoddart (ECE), Harrison Ward (ECE), Kevin Winchell (ECE)
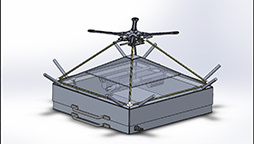
The goal of this project is to create a system which allows a drone upon landing to autonomously dock with, and be secured to a ground based landing pad. The drone will include a control system and sensor suite that is able to detect the landing location, maneuver itself toward, and align itself with the landing pad. The landing pad will then mechanically secure the drone once the landing procedure is complete. When the drone is ready to leave the landing pad, the process will happen in reverse and allow autonomous flight to once again occur.
Team Members: Christopher Bowman (ECE), Charles Kaui (ECE) , Nicholas King (ME), Bryce Kirklen (ME), Cesar Nuno-Banuelos (ME), Angelo Peck (ECE), Chanthol Phea (ECE), Robert Spiers (ME), Nathaniel Thomas (ME), Fady Yousif (ECE)
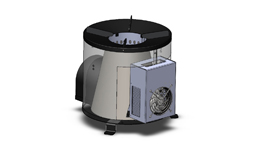
This project suppports SDSU materials research through the innovative design, fabrication and testing of a new Tensile Tester. This Tensile Tester is inteded for use within a Scanning Electron Microscopy to observe fracture and deformation of aluminum and magnesium specimens.
Team Members: Osvaldo Chavarin, Peterson Firth Christopher Guzman Deven Harrington, Christian Hernandez
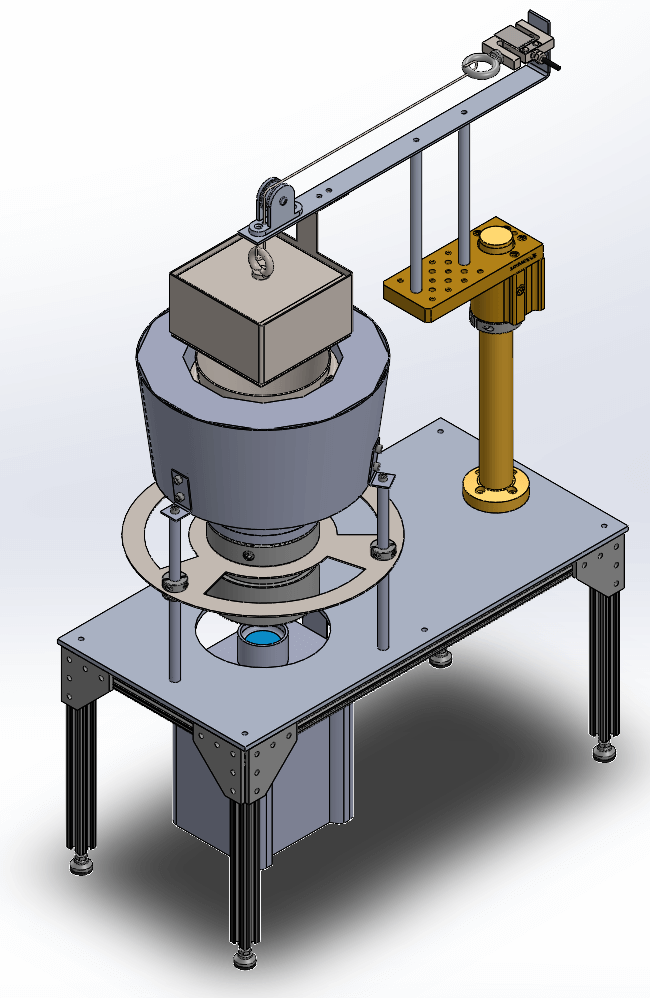
A cone calorimeter is a standard test that evaluates a material’s flammability properties. Ignite Innovation designed an inverted cone calorimeter that simulates conditions consistent with a microgravity environment. Unlike the standard cone calorimeter, this apparatus will impose a slow laminar flow on the sample while reducing the effects of natural convection cooling. The inverted cone calorimeter has potential applications to study materials used in space.
Team Members: Cruz Alarcon, Cheyenne Greer-Potts, Leonardo Montes De Oca Anna Pieroni, Christopher Tapia
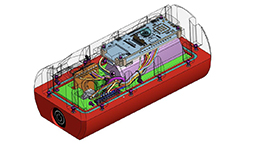
Marines require a sophisticated understanding of where adversary forces are located within their battlespace. The USMC small ground sensor project can provide the Marine ground forces with a deployable compact sensor system that includes audio, visual, seismic, and GPS data to fully understand an evolving battlespace. The Phase 2 teams focus is on optimizing the form factor, reliability, durability, weight, and performance.
Team Members: Mohammed Alfailakawi (ECE) Dwight Anthony Diesmo (ECE) Jhovanna Garcia (ME) Nathan Mincks (ME) John Pawlak (ME) Marcos Rodriguez (ME) Kaylin Sabado (ME) John Sadiq (ME) Nina Truong (ECE) Riley Turner (ECE)
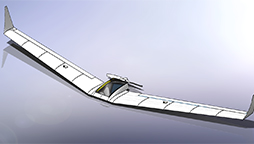
This team performed research, analysis, and testing to design and manufacture a fully 3D printed RC aircraft with the purpose of winning both the Most Innovative Design and Longest Duration of Flight awards in the fixed-wing category at the 6th Annual 3D Printed Aircraft Competition held in July at the University of Texas Arlington. All lifting surfaces and aircraft components must be 3D printed, except for electronics, the propeller, and some hardware. The aircraft is allowed to be powered for only 8 secs and must fly under a 30 ft altitude.
Team Members: Joyce Huang, Jesus Ibarra, Daryl Lyons, Maria Patrisha Perez, Alexander Williamson
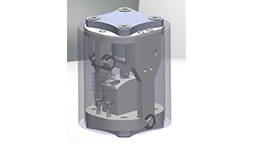
Stefan Leroy a 29 year old army vet sustained a left above the knee amputation and a right below the knee amputation. Our team created a prosthetic ankle that could be placed above the walking foot without altering the users current height. The ankle provides a change in the angle of attack suitable enough to allow for light running or exercises without the need to switch prosthetic feet. The device is triggered remotely and is spring loaded to allow for smooth & convenient transitions.
Team Members: Gillian Drees, Ysabel Murguia, Vernon Pineda, Nathaniel Prince, Thomas Tilk
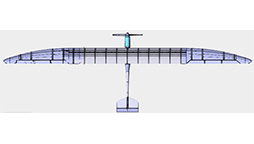
The goal of this project is to design an entirely 3D-printed aircraft (excluding the propeller and electronics) that maximizes glide duration. The motor power may only be used during the initial 8 seconds of flight.
Team Members:
Scarlett Alexander, Daisy Cuevas, Daniel Hernandez Arzate, Kyle Higa, Michael Lennon